Unreliable electrical systems put your facility at risk. Don’t wait for a fault to cause downtime, fire hazards, or costly damage—detect issues before they escalate with acoustic imaging.
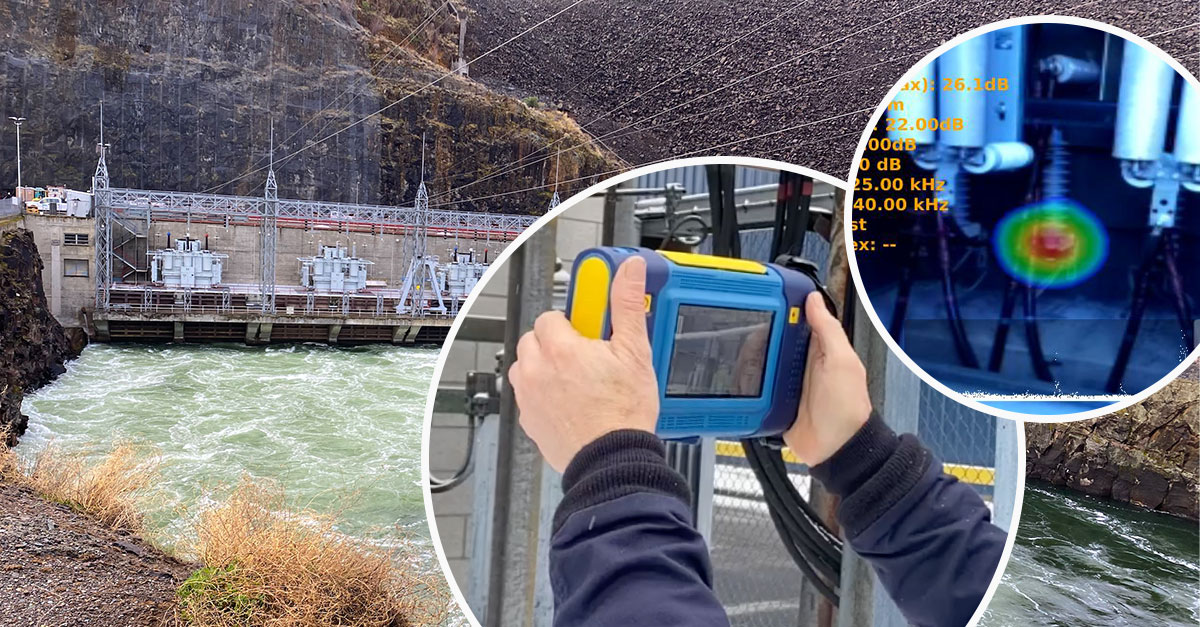
What Are Electrical Failures Costing You?
Electrical faults like arcing, tracking, and corona discharge don’t just cause unexpected outages—they damage equipment, disrupt critical processes, and create serious safety risks for your team. When these issues go unnoticed, you risk:
Expensive Unplanned Downtime: Production stoppages and disruptions to critical processes can cause significant delays.
Costly Equipment Failure: Total electrical failures are extremely expensive, and replacement parts may take a long time to arrive.
Dangerous Work Environment: Electrical faults increase safety risks, potentially leading to fires, explosions, and unsafe conditions for personnel.
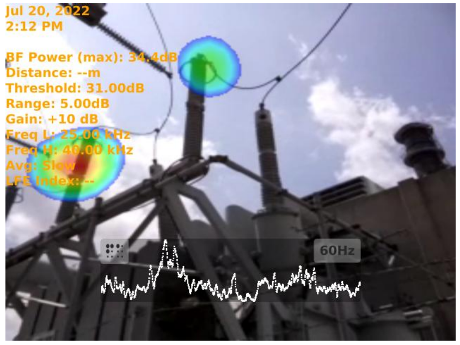
Ultrasound Monitoring for Electrical Defect Detection
Electrical defects like arcing, tracking, and corona discharge produce ultrasound due to the turbulent movement of air particles. Here’s how it works:
Corona discharge happens when high-voltage equipment ionizes the air around it, creating a tiny but rapid flow of current. This ionization causes small shockwaves in the air, emitting high-frequency sound—ultrasound—that’s inaudible to the human ear.
Tracking occurs when electrical discharge follows a path along insulation, degrading the material over time. The discharge creates tiny plasma arcs, generating both heat and high-frequency sound waves.
Arcing involves a visible discharge of electricity between two points. The rapid, unstable release of energy causes air molecules to vibrate, again producing ultrasound as a byproduct.
Since these faults generate high-frequency signals before there’s any noticeable heat buildup, ultrasound is often the earliest sign of an electrical problem—allowing you to detect and fix issues long before thermal methods pick them up.
See Electrical Faults in Real Time with Acoustic Imaging
Acoustic imaging cameras capture the high-frequency signals produced by medium and high-voltage electrical defects — like arcing, tracking, and corona discharge.
This non-contact method works safely in high-voltage environments, giving you a real-time visual of your system’s health and providing key insights to schedule repairs.
- Long Detection Range: Spot electrical faults from up to 200 meters away, keeping you at a safe distance.
- Effortless Reporting: Instantly capture images, tag fault locations, and generate reports to prioritize repairs and share with your team.
- Early Fault Detection: Ultrasound is often the first indicator of electrical defects. High-voltage issues like corona discharge produce no heat, making them invisible to IR cameras — but easily detectable in the ultrasonic range.
- Versatile applications: Ideal for MCC cabinet inspections, overhead power lines, substations, switchgear, transformers, and more.
Electrical System Inspection Process
Plan Your Electrical Survey
Start with a clear plan—map out key inspection points like MCC cabinets, transformers, insulators, and air gaps. Identify areas prone to electrical discharge to ensure no critical asset is overlooked.
Scan, Listen, and Analyze
Use acoustic imaging to detect ultrasonic blooms—the telltale signs of arcing, tracking, or corona. Pair this with Bluetooth headphones to audibly confirm faults and leverage onboard analysis tools like PRPD (Phase Resolved Partial Discharge) patterns to classify the type and severity of the defect.
Capture, Report, and Act
Once a defect is spotted, capture an image, tag the location, and use built-in reporting software to document your findings. Schedule repairs before these minor issues escalate into costly failures or unplanned downtime.
Protect Your Facility from Electrical Failures
Don’t wait for an electrical fault to cause damage. Request a Demo Today to see how our acoustic imaging solutions can help you detect and prevent electrical failures before they happen.
Trusted by Electrical Maintenance & Reliability Teams
Our clients across utilities, manufacturing, and industrial sectors rely on our acoustic imaging cameras for fast, accurate fault detection. From inspecting MCC cabinets to monitoring overhead power lines and substations, our solutions deliver safety and reliability.